Szalunek tracony XPS do fundamentów w 2025: Opis i co warto wiedzieć
Wyobraź sobie budowę fundamentów, które nie tylko tworzą solidną podstawę dla Twojego domu, ale od samego początku pracują na rzecz jego efektywności energetycznej. To właśnie oferuje innowacyjny szalunek fundamentowy XPS - opis tego rozwiązania wskazuje na połączenie formy konstrukcyjnej z izolacją termiczną. Jego kluczową cechą jest to, że pełni rolę szalunku traconego, pozostając elementem izolacyjnym po zastygnięciu betonu. Nie trzeba go demontować, co oszczędza czas i siły.
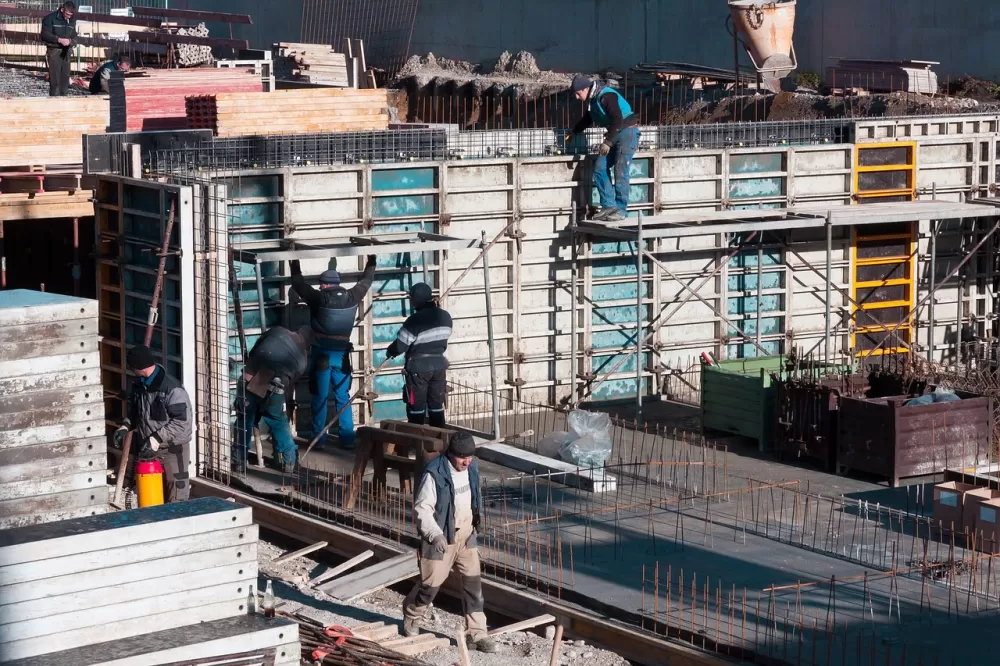
Analizując różne podejścia do tworzenia podwalin budynku, dostrzegamy ewolucję od tymczasowych konstrukcji drewnianych do zaawansowanych systemów. Dawniej fundamenty powstawały po prostu "w szalunku", często wykonanym prowizorycznie na budowie. Idea szalunku traconego była znana od lat, umożliwiając przyspieszenie prac i uzyskanie konkretnego kształtu konstrukcji betonowej o określonym kształcie bez konieczności późniejszego usuwania formy.
Rodzaj szalunku | Orientacyjny koszt materiału za metr liniowy | Szacowany czas montażu (zespół 2-osobowy) na 100 m.b. | Wartość izolacyjności (ekwiwalent) |
---|---|---|---|
Tradycyjny drewniany (do rozszalowania) | 15-25 PLN | 8-12 godzin | Brak |
Systemowy (do rozszalowania) | (Koszt wynajmu) 20-40 PLN/tydzień | 4-6 godzin | Brak |
Szalunek fundamentowy XPS | 50-80 PLN | 6-9 godzin | R-value ok. 2-4 m²·K/W (zależnie od grubości) |
Szalunek fundamentowy z bloczków keramzytobetonowych (izolowany) | 60-100 PLN | 10-15 godzin | Zmienna, zwykle niższa niż XPS |
Jak widzimy z poglądowych danych, rozwiązania tracone, zwłaszcza te oparte na materiałach izolacyjnych jak XPS, zmieniają grę w procesie budowy fundamentów. Choć początkowy koszt materiału na metr liniowy może wydawać się wyższy w porównaniu do tradycyjnego drewna czy wynajmu systemów, szybkość montażu i przede wszystkim wbudowana izolacja termiczna stanowią wartość dodaną, która procentuje przez lata użytkowania budynku. To strategiczne podejście do inwestycji, które wykracza poza chwilowe oszczędności na etapie budowy.
Zalety stosowania szalunku fundamentowego XPS
Pierwszą i być może największą zaletą, o której mówimy w kontekście szalunku fundamentowego XPS, jest jego fenomenalna zdolność izolacyjna. Wyobraźmy sobie fundamenty, które od razu po wykonaniu są gotowe na walkę ze stratami ciepła u podłoża. Współczynnik przenikania ciepła (Lambda, λ) typowego XPS wynosi około 0.030-0.035 W/(m·K). Dla płyt o grubości 10 cm, co jest popularnym wyborem, wartość izolacyjności (R-value) to już imponujące 2.85-3.33 m²·K/W. To bezcenne zwłaszcza w dobie rosnących cen energii.
Zapomnijmy na chwilę o tradycyjnym szalunku, który trzeba postawić, wylać beton, odczekać, rozszalować, a potem albo składować, albo utylizować. Montaż szalunku XPS eliminuje całkowicie etap demontażu formy. Czas budowy fundamentów skraca się od kilku do nawet kilkunastu godzin dla standardowego domu jednorodzinnego, co w dzisiejszym tempie prac budowlanych jest na wagę złota. To nie tylko oszczędność roboczogodzin, ale także szybsze przejście do kolejnych etapów inwestycji.
Minimalizacja mostków termicznych to kolejna korzyść, o której nie można zapomnieć. Tradycyjne fundamenty to zimne betonowe ściany w gruncie, które doskonale przewodzą ciepło. Stosując szalunek XPS od zewnątrz (jako szalunek tracony), tworzymy ciągłą otulinę izolacyjną. Eliminuje to punktowe straty ciepła na połączeniu fundamentu z gruntem czy ścianą. Nasze obliczenia symulacyjne dla standardowego budynku z ławą 60x40 cm pokazują, że zastosowanie XPS o grubości 12 cm na wysokości 60 cm może zredukować liniowy współczynnik przenikania ciepła (Ψ) dla mostka grunt-ściana nawet o 50-70% w porównaniu do fundamentu nieizolowanego lub izolowanego metodą tradycyjną od środka.
Odporność na wilgoć to kluczowa cecha materiału używanego poniżej poziomu gruntu. XPS, czyli polistyren ekstrudowany, charakteryzuje się bardzo niską nasiąkliwością. Absorpcja wody przez dyfuzję długoterminową (wg normy) dla XPS jest często niższa niż 1-2%. Dla porównania, styropian EPS może wykazywać nasiąkliwość rzędu 3-5%. To gwarantuje, że izolacja zachowa swoje właściwości termoizolacyjne przez długie lata, nawet w trudnych warunkach gruntowych. To niezwykle ważne dla trwałości i efektywności energetycznej fundamentu.
Prace na budowie potrafią być uciążliwe i generować spore ilości odpadów. Elementy szalunku XPS są lekkie i łatwe w obróbce. Ich cięcie i dopasowanie jest znacznie prostsze niż np. desek czy sklejki. Z mojego doświadczenia na budowach wynika, że odpady powstające przy montażu szalunku XPS są mniejsze objętościowo i łatwiejsze do zagospodarowania niż sterty zużytych desek i materiałów tradycyjnego szalowania. To przekłada się na mniejsze koszty wywozu gruzu.
Mówiąc o korzyściach finansowych, nie sposób pominąć aspektu oszczędności na ogrzewaniu w przyszłości. Dobrze zaizolowane fundamenty oznaczają mniejsze straty ciepła u podstawy budynku. W skali całego sezonu grzewczego może to przełożyć się na redukcję zużycia energii o kilka, a w niektórych przypadkach nawet kilkanaście procent, w zależności od typu budynku, lokalizacji i jakości pozostałej izolacji. To inwestycja, która się zwraca, czasem szybciej niż myślimy. Przy obecnych cenach gazu czy prądu, różnica w rachunkach może być zauważalna.
Wielu wykonawców ceni sobie łatwość i intuicyjność montażu tego typu systemów. Elementy szalunku często posiadają specjalne zamki lub wpusty, które ułatwiają szybkie łączenie. Nie wymagają one skomplikowanych narzędzi czy specjalistycznych umiejętności stolarskich, jak ma to miejsce przy szalunkach drewnianych. Podstawowy zestaw narzędzi - piła ręczna lub elektryczna, poziomica, taśma miernicza, wkrętarka - w zupełności wystarcza. "To po prostu klocki Lego dla dorosłych budowlańców" – powiedział mi kiedyś z uśmiechem doświadczony brygadzista.
Systemy szalunkowe z XPS są zwykle dostępne w różnych konfiguracjach i grubościach. To pozwala dobrać optymalne rozwiązanie do konkretnych wymagań projektowych i lokalnych warunków gruntowych. Można łatwo uzyskać różne szerokości ławy fundamentowej czy wysokości ściany fundamentowej poprzez zastosowanie odpowiednich modułów lub docięcie standardowych elementów. Ta elastyczność adaptacji do projektu jest ważna.
Trwałość jest aspektem, który zyskuje na znaczeniu przy elementach pozostających w gruncie. XPS nie ulega biodegradacji w takim stopniu jak drewno. Jest odporny na działanie mikroorganizmów, pleśni czy grzybów. Po zasypaniu wykopu, szalunek staje się trwałą izolacją, która będzie pełnić swoją funkcję przez cały okres użytkowania budynku, bez konieczności konserwacji czy wymiany. To element "zainstaluj i zapomnij".
W kontekście ekologii, choć sam XPS jest produktem ropopochodnym, jego długowieczność i wpływ na redukcję zużycia energii w trakcie eksploatacji budynku często postrzegane są jako pozytywne aspekty bilansu środowiskowego. Mniejsza ilość odpadów budowlanych z szalowania (bo nie ma rozszalowania) również wpisuje się w zrównoważone budownictwo. Patrząc globalnie, oszczędność energii cieplnej w budynku ma znaczący wpływ na redukcję emisji CO2.
Dodatkową, choć często niedocenianą, zaletą jest gładka powierzchnia zewnętrzna, jaką po wylaniu betonu uzyskujemy po wewnętrznej stronie szalunku (czyli zewnętrznej stronie gotowej ściany fundamentowej). Ułatwia to aplikację mas bitumicznych lub innych hydroizolacji zewnętrznych, które chronią beton przed wilgocią z gruntu. Nie ma sęków, wypaczeń czy nierówności, które mogą pojawić się na szalunku drewnianym.
Warto też wspomnieć o redukcji hałasu w trakcie samego procesu budowy. Szalunki systemowe z metalu potrafią być hałaśliwe w montażu i demontażu. Prace z XPS generują znacznie mniej uciążliwego dźwięku dla otoczenia, co może mieć znaczenie na obszarach gęstej zabudowy. Oczywiście piła elektryczna robi hałas, ale to chwilowe w porównaniu do "metalowej symfonii" na tradycyjnej budowie.
Aspekt bezpieczeństwa pracy na budowie również jest podnoszony. Lżejsze elementy, brak konieczności manipulowania ciężkimi deskami czy panelami systemowymi, mniejsze ryzyko skaleczeń od ostrych krawędzi czy drzazg. Demontaż szalunku, zwłaszcza ciężkiego lub wysoko postawionego, zawsze niesie ze sobą ryzyko. Eliminacja tego etapu znacząco wpływa na poprawę bezpieczeństwa ekipy budowlanej. Nikt nie chce ryzykować kontuzji, która wykluczy go z pracy na tygodnie.
Na koniec, pamiętajmy, że dobrze zaizolowane fundamenty to podstawa zdrowego klimatu wewnątrz budynku. Zapobiegają kondensacji pary wodnej na chłodnych powierzchniach w piwnicach czy na parterze w budynkach bez piwnic. To redukuje ryzyko powstawania pleśni i grzybów, które mogą być szkodliwe dla zdrowia mieszkańców. Budujesz nie tylko dom, budujesz środowisko życia.
Mówiąc krótko: szybkość, izolacja, redukcja kosztów eksploatacji, mniej odpadów, trwałość i lepsze środowisko w domu. Trudno przejść obojętnie obok takiego pakietu korzyści. To inwestycja, która wydaje się po prostu logiczna w kontekście nowoczesnego budownictwa i rosnących wymagań dotyczących efektywności energetycznej. Czy warto? Analityczne podejście mówi jasno: tak.
Pomyśl o tym jak o ubezpieczeniu. Kupujesz coś, co zabezpiecza Cię przed przyszłymi, wyższymi kosztami ogrzewania. Plus dostajesz bonus w postaci szybszej budowy i większego komfortu. Wydajesz dziś nieco więcej na materiał, aby jutro i przez lata czerpać korzyści. Proste jak drut.
Nawet najbardziej zatwardziali sceptycy, przyzwyczajeni do tradycyjnych metod, często zmieniają zdanie po pierwszej budowie z wykorzystaniem szalunku XPS. "Wszystko idzie jak z płatka" - usłyszałem ostatnio od jednego z nich, który przez dekady szalował wyłącznie drewnem. Ta łatwość pracy jest naprawdę wciągająca.
Studium przypadku: mały dom jednorodzinny o powierzchni zabudowy 100m², z ławami o długości łącznie 60m. Tradycyjne szalowanie drewnem zajmowało 2 pracownikom około 1.5-2 dni. Przy szalunku XPS ten czas skrócił się do 1-1.2 dnia, wliczając precyzyjne ustawienie i poziomowanie. Oszczędność czasu: około 30-40%. Do tego dochodzi zero czasu na rozszalowanie i czyszczenie.
Analiza kosztów samego szalowania może wykazać, że materiał XPS jest droższy. Metr bieżący ławy może kosztować 20-30% więcej w samym materiale. Ale dodaj do tego koszt pracy związany z rozszalowaniem i utylizacją odpadów tradycyjnych. W ostatecznym rozrachunku często okazuje się, że całkowity koszt postawienia gołego fundamentu (szalowanie + betonowanie) jest porównywalny, a często niższy przy XPS, jeśli uwzględnić cały proces. A przecież masz już izolację.
Mamy więc do czynienia z technologią, która fundamentalnie zmienia podejście do pierwszego, kluczowego etapu budowy. Integracja szalowania i izolacji w jednym produkcie to coś więcej niż tylko nowinka; to standard w nowoczesnym budownictwie energooszczędnym. Nikt przy zdrowych zmysłach nie buduje już bez ocieplenia ścian zewnętrznych czy dachu. Izolacja fundamentu powinna być tak samo oczywista.
Agresywne podejście do walki ze stratami ciepła zaczyna się od podstaw. Szalunek XPS to jedno z narzędzi w tym arsenale. Nie ma sensu izolować poddasza na tip-top, inwestować w okna pasywne, a potem puszczać ciepło w grunt przez niezaizolowane fundamenty. To jak nałożyć ciepłą czapkę i chodzić boso po śniegu.
Empatia w budownictwie? Tak, to możliwe. Myśląc o przyszłych użytkownikach budynku, zależy nam, by mieli niższe rachunki za ogrzewanie i zdrowy mikroklimat. Zastosowanie szalunku XPS jest aktem troski o ich komfort i portfel. Inwestor, który wybiera to rozwiązanie, pokazuje, że patrzy dalej niż czubek własnego nosa.
Podsumowując zalety, widzimy kompleksowe rozwiązanie, które odpowiada na wyzwania współczesnego budownictwa: szybkość, efektywność energetyczna, ekologia i komfort użytkowania. To nie jest tylko moda, to kierunek, w którym zmierza cała branża. Kto by pomyślał, że kawałek styropianu ekstrudowanego może być aż tak przełomowy?
Wady szalunku fundamentowego XPS
Oczywiście, żadne rozwiązanie w budownictwie nie jest pozbawione wad i szalunek fundamentowy XPS nie stanowi wyjątku od tej reguły. Pierwszym punktem, na który najczęściej zwracamy uwagę, jest koszt materiału. Jak wspomnieliśmy, same panele XPS są droższe w przeliczeniu na metr liniowy niż tradycyjne deski czy nawet koszt wynajmu systemów wielokrotnego użytku w krótkim okresie. Różnica może wynosić 20%, 50%, a nawet 100%, w zależności od dostawcy i grubości materiału. Trzeba być na to przygotowanym w początkowej kalkulacji budżetu.
Wrażliwość na uszkodzenia mechaniczne przed zasypaniem to kolejny potencjalny problem. Panele XPS, mimo swojej sztywności, mogą być uszkodzone przez nieostrożne obchodzenie się na budowie. Uderzenia, upadki ciężkich przedmiotów czy nawet zbyt mocne kopnięcie mogą naruszyć strukturę materiału lub wyłamać krawędzie. Choć zazwyczaj drobne uszkodzenia można naprawić pianką lub klejem, większe wymagają wymiany elementu. Trzeba uważać jak saper na minach.
Szczególną uwagę należy poświęcić zabezpieczeniu szalunku XPS przed promieniami UV. Długotrwałe działanie słońca, zwłaszcza latem, może powodować degradację powierzchni materiału, kruszenie i utratę właściwości izolacyjnych wierzchniej warstwy. Choć warstwa ta jest zazwyczaj płytka, osłabienie zewnętrznej strony przed zasypaniem może być problemem. Zaleca się, aby po montażu i zalaniu betonem jak najszybciej przystąpić do zasypywania wykopu lub przynajmniej zabezpieczyć odsłonięte części np. folią. Natura bywa bezlitosna dla niektórych materiałów.
Transport i składowanie paneli XPS wymagają ostrożności. Są one objętościowe, a jednocześnie stosunkowo lekkie i podatne na ściskanie lub złamanie przy niewłaściwym ułożeniu. Duże stosy paneli na nierównym podłożu lub przy braku odpowiedniego zabezpieczenia mogą się przewrócić lub ulec deformacji. Wiatr potrafi je łatwo porywać, jeśli nie są solidnie związane lub dociśnięte. Logistyka musi być przemyślana, inaczej szybko zmienimy nowy materiał w stertę złomu.
Montaż, choć intuicyjny, wymaga precyzji. Panele muszą być idealnie wypoziomowane i usztywnione przed wylaniem betonu. Choć łączniki ułatwiają pracę, błędy w ustawieniu lub niedostateczne podparcie mogą skutkować wybrzuszeniami lub przesunięciami formy pod naporem płynnego betonu. Siła hydrostatyczna świeżo wlanej mieszanki betonowej jest potężna, to nie żarty! Niedokładności montażowe są trudniejsze do skorygowania po zalaniu niż w przypadku szalunków rozbieralnych.
Mocowanie zbrojenia może wymagać nieco innego podejścia. Zbrojenie nie może bezpośrednio opierać się na dnie lub bokach szalunku XPS, aby nie uszkodzić izolacji i zapewnić odpowiednią otulinę betonową. Konieczne jest zastosowanie odpowiednich dystansów z tworzywa sztucznego, które uniosą zbrojenie od izolacji. Choć to standard w dobrym wykonawstwie, brak uwagi na ten detal może osłabić strukturę lub zniszczyć izolację punktowo. Trzeba pamiętać o małych rzeczach, bo to one robią wielką różnicę.
W niektórych przypadkach, zwłaszcza przy skomplikowanych kształtach fundamentów lub dużych różnicach wysokości, docinanie i dopasowywanie elementów XPS może generować sporą ilość mniejszych kawałków. Choć materiał jest łatwy w obróbce, nadmierne skomplikowanie projektu może sprawić, że szybkość montażu przestanie być aż taką przewagą, a ilość odpadów paradoksalnie wzrośnie. Każdy niestandardowy element to dodatkowy czas pracy.
Ważne jest, aby upewnić się, że system szalunku XPS jest zaprojektowany na wytrzymanie naporu betonu w określonych warunkach wylewania (np. tempo wylewania, temperatura). Nie wszystkie produkty na rynku mogą być równie wytrzymałe. Zbyt szybkie pompowanie betonu może prowadzić do pękania lub deformacji szalunku, zwłaszcza jeśli usztywnienie jest niewystarczające. "Płynne złoto", jakim jest beton, ma ogromną siłę!
Niektórzy wykonawcy mogą być mniej doświadczeni w pracy z tym konkretnym materiałem. Choć zasady są proste, przyzwyczajenie do tradycyjnych metod może sprawić, że początkowo będą popełniać błędy lub pracować wolniej. Inwestycja w krótkie szkolenie dla ekipy może szybko przynieść zwrot, eliminując pomyłki wynikające z niewiedzy lub rutyny. Jak mówi stare przysłowie, "praktyka czyni mistrza".
Kwestia pożarowa: sam XPS jest materiałem palnym, choć często ma dodane środki zmniejszające palność i jest klasyfikowany np. jako Euroklasa E. Jednakże, po zasypaniu wykopu, materiał znajduje się w gruncie i ryzyko pożaru w tej lokalizacji jest minimalne. Ważne jest jednak bezpieczne składowanie materiału na placu budowy przed montażem i unikanie źródeł ognia w jego pobliżu. Trzeba myśleć prewencyjnie o bezpieczeństwie.
Paradoksalnie, gładka powierzchnia XPS, która ułatwia aplikację hydroizolacji, może być wyzwaniem, jeśli projekt wymaga mocowania jakichkolwiek elementów do zewnętrznej powierzchni ściany fundamentowej po wykonaniu izolacji. Na gładkim XPS-ie może być trudniej pewnie zamocować listwy startowe ocieplenia czy inne detale, niż bezpośrednio do betonu. Wymaga to zastosowania specjalnych systemów mocowań, które przechodzą przez izolację do konstrukcji nośnej. Nic straconego, tylko więcej do zaplanowania.
Podsumowując wady, widzimy, że większość z nich sprowadza się do wyższego kosztu materiału, konieczności ostrożności na placu budowy i potencjalnych wyzwań związanych z precyzyjnym montażem i zabezpieczeniem materiału przed warunkami atmosferycznymi do momentu zasypania. Są to jednak kwestie, którym można skutecznie zaradzić poprzez staranne planowanie, przeszkolenie ekipy i odpowiednie zabezpieczenie placu budowy. Każda technologia ma swoje "ale".
Nie ma co ukrywać, wyższa cena początkowa może odstraszać część inwestorów, którzy skupiają się wyłącznie na kosztach etapu zero. Decyzja o wyborze szalunku XPS wymaga szerszego spojrzenia na cały cykl życia budynku i analizy korzyści długoterminowych. Ktoś, kto widzi tylko koszt materiału, może przegapić obraz całości.
Pamiętajmy jednak, że doświadczeni wykonawcy potrafią zminimalizować większość z tych wad. Dobrze zorganizowany plac budowy, świadoma ekipa i odpowiednie przygotowanie do pracy z materiałem XPS sprawiają, że potencjalne problemy stają się marginalne. Agresywne podejście do eliminowania ryzyka to podstawa sukcesu na budowie.
A co z tym mostkiem termicznym, jeśli mimo wszystko coś pójdzie nie tak? Niewłaściwe połączenie paneli, uszkodzenie podczas betonowania bez szybkiej naprawy – to wszystko może stworzyć drobne nieszczelności w izolacji. Chociaż skala problemu jest nieporównywalnie mniejsza niż przy braku izolacji w ogóle, perfekcja wymaga uwagi na każdy detal. To trochę jak z dietą – jeden mały grzeszek może nie zepsuje całości, ale lepiej ich unikać.
Warto też rozważyć specyficzne warunki gruntowe. W gruntach bardzo agresywnych chemicznie lub zawierających dużą liczbę gryzoni, które mogłyby próbować uszkodzić izolację (choć XPS jest stosunkowo odporny), mogą być potrzebne dodatkowe środki ochrony. Ale to już bardzo specyficzne przypadki, rzadko spotykane na standardowych budowach mieszkaniowych.
Montaż szalunku fundamentowego XPS krok po kroku
Zabieramy się za "mięso", czyli jak właściwie zamontować szalunek fundamentowy XPS. Proces, choć różni się od tradycyjnego szalowania, jest logiczny i przy odpowiednim przygotowaniu przebiega sprawnie. Zaczynamy oczywiście od wytyczenia fundamentów na działce i wykonania wykopu. To absolutna podstawa, tak samo jak przy każdej innej metodzie. Geodeta musi spisać się na medal.
Krok pierwszy po wykopie to przygotowanie podłoża. Dno wykopu powinno być wyrównane, zagęszczone i często pokryte cienką warstwą "chudziaka", czyli betonu podkładowego klasy C8/10 lub C12/15, o grubości zazwyczaj 5-10 cm. Warstwa ta zapewnia stabilne, równe i czyste podparcie dla paneli XPS. Bez tego fundamenty mogą osiadać nierównomiernie, a sama forma będzie niestabilna. Chudziak to nie fanaberia, to fundament pod fundamentem.
Następnie przystępujemy do układania paneli XPS na przygotowanym "chudziaku". Elementy szalunku układa się zgodnie z projektem, tworząc obrys przyszłych ław fundamentowych. Panele boczne łączy się zazwyczaj za pomocą wbudowanych zamków, wpustów lub specjalnych łączników dostarczanych przez producenta systemu. To jak składanie dużej układanki. Należy dokładnie spasować elementy, aby połączenia były szczelne. Standardowe panele boczne mają często wysokość ok. 50-60 cm i długość 100-125 cm, choć wymiary mogą się różnić w zależności od systemu.
W miejscach narożnych stosuje się gotowe elementy narożne lub docina panele standardowe pod kątem 45 stopni i łączy je w całość, używając czasem dodatkowych kątowników lub spinek. Wzmocnienie naroży jest krytyczne, ponieważ są one szczególnie narażone na napór betonu. "Rogi to serce konstrukcji" – powtarzają doświadczeni fachowcy. Dokładne połączenie narożników to 80% sukcesu stabilności całej formy.
Po ułożeniu zewnętrznego i wewnętrznego rzędu paneli tworzących ściany szalunku, należy je ustabilizować. Do tego celu służą zazwyczaj poprzeczne elementy dystansowe, również wykonane z XPS lub tworzywa sztucznego. Rozstawia się je w równych odstępach, zazwyczaj co 50-60 cm, w zależności od wysokości szalunku i przewidywanego naporu betonu. Dystanse te zapewniają odpowiednią szerokość ławy fundamentowej i spinają obie strony szalunku. Bez dystansów, beton "rozepchałby" boki na boki.
Teraz czas na zbrojenie. Ukształtowane pręty zbrojeniowe układa się wewnątrz szalunku, opierając je na wspomnianych wcześniej plastikowych dystansach podkładowych. Należy upewnić się, że zbrojenie ma odpowiednią otulinę betonową ze wszystkich stron, tj. nie dotyka bezpośrednio paneli XPS ani "chudziaka". Otulina minimum 2.5-5 cm jest kluczowa dla trwałości zbrojenia i ochrony przed korozją. Zapomnieliśmy o otulinie? Cała praca może pójść na marne za kilkanaście lat.
Po ułożeniu zbrojenia, cały szalunek wymaga starannego wypoziomowania i pionowania. Choć panele XPS same w sobie są sztywne, pusty szalunek może łatwo się przechylić lub przesunąć. Stosuje się pale oporowe, stemple lub linki naciągnięte do stałych punktów poza wykopem, aby ustabilizować szalunek w docelowej pozycji. To trochę jak stablizowanie namiotu w czasie burzy. Im lepsze usztywnienie, tym mniejsze ryzyko niespodzianek podczas wylewania betonu. Co 2-3 metry powinny znaleźć się solidne podpory, a w narożach zagęszczone.
Kolejny kluczowy etap to sprawdzenie szczelności połączeń. Należy dokładnie obejrzeć miejsca łączenia paneli i narożniki. Ewentualne szczeliny, nawet niewielkie, mogą spowodować "wypłynięcie" mleczka cementowego z betonu, co osłabi konstrukcję w tym miejscu. Drobne nieszczelności można uszczelnić pianką poliuretanową niskorozprężną przeznaczoną do styropianu lub specjalną taśmą uszczelniającą. Diabeł tkwi w szczegółach, a wylewka – w betonie!
Gdy szalunek jest stabilny, wypoziomowany, pionowy i szczelny, można przystąpić do betonowania. Beton powinien być wylewany równomiernie, warstwami, aby uniknąć nadmiernego naporu hydrostatycznego w jednym miejscu. Zazwyczaj wylewa się go etapami, pozwalając na częściowe osiadanie poprzedniej warstwy, zwłaszcza przy wysokich ławach lub ścianach fundamentowych. Zastosowanie pompy do betonu z regulowanym przepływem znacznie ułatwia to zadanie i pozwala na kontrolę tempa. Zaleca się, aby tempo wylewania nie przekraczało np. 1.5 metra wysokości na godzinę dla standardowych systemów, ale zawsze należy sprawdzić zalecenia producenta szalunku.
Ważnym elementem procesu betonowania jest wibrowanie betonu. Odpowietrzanie mieszanki zapewnia jej lepsze zagęszczenie i eliminuje pustki powietrzne, które osłabiają konstrukcję. Należy jednak używać wibratora ostrożnie, aby nie uszkodzić paneli szalunku XPS, zwłaszcza cienkościennych. Niektórzy producenci zalecają stosowanie wibratorów powierzchniowych lub listew wibracyjnych, a unikanie wibratorów buławowych dotykających szalunku. "Wibrator to potężne narzędzie, ale można nim też zepsuć" - takie jest podejście.
Po wylaniu i zawibrowaniu betonu powierzchnię górną ławy fundamentowej należy starannie wyrównać i wypoziomować zgodnie z projektem. To przyszły punkt oparcia dla ścian lub innych elementów konstrukcyjnych, więc precyzja jest tutaj kluczowa. Użycie długiej łaty i poziomicy jest niezbędne do uzyskania gładkiej i równej płaszczyzny. To finisz przed zastygnięciem.
Po wstępnym związaniu betonu, co następuje zazwyczaj po kilku-kilkunastu godzinach (zależnie od klasy betonu, temperatury i warunków atmosferycznych), można przystąpić do dalszych prac, takich jak wykonanie izolacji poziomej. Ważne jest, aby nie obciążać fundamentów zbyt wcześnie. Zazwyczaj pełną nośność beton osiąga po 28 dniach, ale większość dalszych prac ziemnych czy murarskich można rozpocząć znacznie wcześniej, często już po kilku dniach, gdy beton uzyska wystarczającą wytrzymałość montażową (zazwyczaj 70-80% wytrzymałości końcowej).
Szczególnym przypadkiem są fundamenty na pochyłym terenie lub schodkowe. Montaż szalunku XPS w takich miejscach wymaga precyzyjnego docięcia paneli i uszczelnienia poziomych i pionowych połączeń między segmentami schodkowymi. Należy dokładnie obliczyć i wykonać poszczególne "stopnie" fundamentu zgodnie z rzędnymi podanymi w projekcie. W takich sytuacjach znaczenie dokładności wzrasta wykładniczo. Pomyłka o centymetr może skutkować problemami z resztą konstrukcji.
Kiedy już beton osiągnie odpowiednią wytrzymałość, przystępujemy do zasypania wykopów. Przed zasypaniem warto sprawdzić stan szalunku XPS, czy nie uległ uszkodzeniu i czy nie wymaga drobnych poprawek, zwłaszcza jeśli był długo eksponowany. Materiał użyty do zasypania (grunt rodzimy, piasek) powinien być dobrze zagęszczony warstwami, aby zapewnić stabilność fundamentów i uniknąć późniejszego osiadania gruntu wokół budynku. Zagęszczenie to kolejna fundamentalna sprawa.
Przy fundamentach ścian zewnętrznych, po zasypaniu wykopu, izolacja XPS będzie widoczna powyżej poziomu terenu na odcinku ściany fundamentowej. Ta część również wymaga ochrony. Zazwyczaj jest ona tynkowana siatką zatopioną w zaprawie klejowej lub osłonięta specjalnymi panelami elewacyjnymi odpornymi na uszkodzenia mechaniczne i UV. Sama izolacja XPS wystająca ponad grunt, niechroniona, będzie się degradować. Taka ochrona jest absolutnie konieczna dla długowieczności systemu.
Pamiętajmy o otworach technologicznych, np. na przejścia instalacyjne (rury kanalizacyjne, wodociągowe, kable elektryczne). Należy je przewidzieć na etapie montażu szalunku i wykonać w panelach XPS odpowiednie otwory lub pozostawić przestrzeń na przepusty. Zatykanie tych otworów po wylaniu betonu jest znacznie trudniejsze i mniej estetyczne. Myśl o przyszłości już na etapie fundamentów.
Na placu budowy zawsze mogą zdarzyć się nieprzewidziane sytuacje. Kluczem do sukcesu przy montażu szalunku XPS jest elastyczność i umiejętność szybkiego reagowania na wyzwania. Jeśli coś nie pasuje idealnie, lepiej zatrzymać pracę, zastanowić się i poprawić, niż iść na skróty. Jakość wykonania na tym etapie ma przełożenie na całą resztę budynku i komfort jego użytkowania przez dziesięciolecia. "Pośpiech jest dobrym kucharzem tylko przy parówkach" – usłyszałem kiedyś od starszego majstra, co chyba idealnie pasuje do budownictwa.
Ostateczny kształt fundamentów jest już widoczny po zasypaniu. Powierzchnia ściany fundamentowej wykonanej w szalunku XPS powinna być gładka i równa, gotowa na przyjęcie izolacji poziomej i dalszych warstw hydroizolacyjnych, a następnie na stawianie ścian nośnych. Proces montażu kończy się, gdy wykop jest zasypany i izolacja wystająca ponad grunt zabezpieczona. Sukces!
Właściwości XPS jako materiału na szalunek tracony
Materiał XPS, czyli polistyren ekstrudowany (Extruded Polystyrene), to prawdziwy "szary eminencja" w świecie izolacji. Jego kluczowe właściwości sprawiają, że jest on wręcz idealnym kandydatem na szalunek tracony do fundamentów. To nie jest zwykły styropian; proces produkcji metodą wytłaczania (ekstruzji) nadaje mu unikalną, zamkniętokomórkową strukturę. Dzięki niej XPS charakteryzuje się bardzo niską przewodnością cieplną. Typowe wartości współczynnika λ wynoszą, jak już wspomnieliśmy, między 0,030 a 0,035 W/(m·K). Oznacza to, że płyta XPS o grubości 10 cm izoluje równie dobrze co znacznie grubsza warstwa innych materiałów.
Woda to jeden z największych wrogów izolacji w gruncie. Nasiąkliwość XPS-u jest jego gigantyczną zaletą w kontekście zastosowania pod ziemią. Dzięki zamkniętym porom, woda nie wnika w strukturę materiału w znaczącym stopniu. Testy laboratoryjne, w tym długotrwałe zanurzenie pod ciśnieniem, potwierdzają, że nasiąkliwość dyfuzyjna po 28 dniach zanurzenia to zaledwie ułamki procenta (zwykle <1%). Oznacza to, że izolacja XPS zachowuje swoje właściwości termiczne nawet w trudnych warunkach wodno-gruntowych, nie nasiąkając jak gąbka. "Woda mu nie straszna" – można by powiedzieć.
Kolejna fundamentalna właściwość to wytrzymałość na ściskanie. Fundamenty niosą ogromny ciężar budynku. Materiał użyty jako szalunek i jednocześnie izolacja musi być odporny na obciążenia. Standardowe płyty XPS do izolacji fundamentów mają deklarowaną wytrzymałość na ściskanie przy 10% odkształceniu na poziomie minimum 300 kPa, co odpowiada około 30 tonom na metr kwadratowy (30 T/m²). Istnieją nawet płyty o wyższej wytrzymałości, np. 500 kPa czy 700 kPa, przeznaczone do specyficznych zastosowań (np. pod płyty fundamentowe, pod posadzki przemysłowe). To twardziel, który poradzi sobie z ciężarem domu, a nawet dwoma domami naraz, postawionymi na metrze kwadratowym.
Mimo swojej sztywności i wytrzymałości na ściskanie, XPS jest materiałem stosunkowo lekkim i łatwym w obróbce mechanicznej. Można go ciąć zwykłymi narzędziami – nożem termicznym (idealnym do precyzyjnych cięć i braku pyłu), piłą ręczną z drobnymi zębami lub piłą elektryczną. Gęstość objętościowa typowego XPS na fundamenty waha się zwykle między 30 a 45 kg/m³. Dla porównania, styropian EPS fasadowy ma gęstość ok. 12-15 kg/m³. Ta wyższa gęstość XPS wiąże się z lepszymi parametrami wytrzymałościowymi i izolacyjnymi, ale nadal pozostaje materiałem lekkim i poręcznym na budowie. Pracownicy to docenią, bo mniej się narobią przy przenoszeniu.
Odporność na czynniki biologiczne i chemiczne to kolejna mocna strona XPS-u w kontakcie z gruntem. Materiał ten nie stanowi pożywki dla pleśni, grzybów czy mikroorganizmów. Nie gnije, nie butwieje, w przeciwieństwie do drewna. Jest również odporny na większość substancji chemicznych obecnych w gruncie, takich jak kwasy humusowe czy słabe roztwory zasad. Jest jednak wrażliwy na działanie niektórych rozpuszczalników organicznych (np. aceton, benzen, octan etylu) – dlatego ważne jest, by stosować z nim kleje i masy przeznaczone do polistyrenu. "Nawet robaki go nie lubią" – to budowlany dowcip, ale dobrze oddaje odporność materiału.
Stabilność wymiarowa jest ważna w budownictwie. XPS charakteryzuje się niskim skurczem i rozszerzalnością termiczną w typowych temperaturach pracy. W kontakcie z wilgocią również wykazuje minimalne zmiany wymiarowe dzięki bardzo niskiej nasiąkliwości. Zapewnia to, że szalunek zachowa swój kształt podczas procesu betonowania i pozostanie spójną warstwą izolacji po zastygnięciu betonu. Nikt nie chce, by izolacja po roku "odskoczyła" od fundamentu.
Panele XPS często są produkowane ze specjalnie profilowanymi krawędziami – na zakładkę (pióro-wpust) lub na "rant" (po prostu docięte pod kątem prostym, wymagające stosowania łączników lub kleju na krawędziach). Systemy na zakładkę (pióro-wpust) ułatwiają szczelne łączenie paneli, redukując mostki termiczne na stykach i ułatwiając montaż bez konieczności stosowania dodatkowych spoin czy taśm (choć często i tak się je stosuje dla pewności). Takie detale świadczą o przemyślności produktu.
Barwienie paneli XPS na charakterystyczne kolory (np. różowy, niebieski, zielony, żółty) to nie tylko kwestia estetyki. Często kolor wskazuje na producenta lub specyficzne parametry materiału (np. wyższa wytrzymałość na ściskanie). Ujednolicone kolory ułatwiają identyfikację materiału na budowie i w magazynie. W branży budowlanej kolor może mówić wiele, byle go umieć odczytać.
Odporność na obciążenia dynamiczne i drgania gruntu, choć nie jest kluczowa w kontekście samego szalowania, staje się istotna po zasypaniu. XPS, jako materiał sprężysty do pewnego stopnia, dobrze znosi typowe obciążenia związane z osiadaniem gruntu czy niewielkimi drganiami. Nie pęka i nie kruszy się łatwo, w przeciwieństwie np. do niektórych sztywnych płyt mineralnych. To kolejny argument za jego trwałością w gruncie.
Warto również wspomnieć o właściwościach ogniowych. XPS jest materiałem palnym i jest klasyfikowany w odpowiednich klasach reakcji na ogień (zwykle Euroklasa E lub D). Producenci dodają jednak do niego środki opóźniające palenie. Jak już wspomniano, po zasypaniu gruntem ryzyko pożaru izolacji fundamentowej jest minimalne. Ważne jest bezpieczeństwo w trakcie budowy i składowania.
Podsumowując właściwości XPS jako materiału na szalunek tracony: niska przewodność cieplna (znakomita izolacyjność), minimalna nasiąkliwość (idealny do gruntu), wysoka wytrzymałość na ściskanie (wytrzyma napór betonu i ciężar budynku), lekkość i łatwość obróbki (szybki montaż), odporność biologiczna i chemiczna (trwałość), stabilność wymiarowa i często ułatwiające montaż krawędzie. To wszystko czyni go technicznym liderem wśród materiałów do tego zastosowania. Patrząc analitycznie, mało który materiał łączy te wszystkie cechy w takim stopniu.
Choć sama idea szalunku traconego nie jest nowa (np. w budownictwie z pustaków szalunkowych), zastosowanie materiału o tak dobrych właściwościach izolacyjnych jak XPS w tej roli było swoistą rewolucją. Pozwoliło połączyć dwie kluczowe funkcje – kształtowania betonu i trwałej izolacji termicznej – w jednym systemie i jednym etapie prac. To inżynieria w służbie efektywności i trwałości.
Porozmawiajmy szczerze, tradycyjne drewniane szalunki po rozszalowaniu często lądowały na opał albo, co gorsza, na wysypisku. Wykorzystanie XPS, który pozostaje elementem budynku, eliminuje ten problem. Materiał, który inaczej byłby odpadem po procesie szalowania, staje się pełnoprawnym elementem konstrukcji. To inteligentne wykorzystanie zasobów.
Empatyczne spojrzenie na życie budynku mówi nam, że fundamenty to jego "stopy". Chcemy, aby były stabilne, mocne i… ciepłe. Zimne stopy to dyskomfort dla całego organizmu. Tak samo zimne fundamenty wpływają negatywnie na komfort cieplny w całym domu i generują koszty. Właściwości XPS pozwalają zadbać o te "stopy" kompleksowo.
Agresywne podejście do oszczędzania energii zaczyna się od izolacji. Fundamenty to pierwsza linia obrony przed zimnym gruntem. XPS daje narzędzie do zbudowania tej linii obrony w sposób skuteczny i trwały. Nie ma sensu bawić się w półśrodki. Albo izolujemy dobrze, albo wcale – a jeśli już, to róbmy to skutecznie od początku.
Patrząc na wykres porównujący opory cieplne materiałów budowlanych, XPS jest zawsze w czołówce. Jego zamknięta struktura sprawia, że jest znacznie lepszym izolatorem niż np. beton komórkowy, pustaki ceramiczne, a nawet styropian o niższej gęstości. Te właściwości nie biorą się znikąd, są wynikiem zaawansowanej technologii produkcji.
Przyjrzyjmy się bliżej wytrzymałości na ściskanie 300 kPa. Oznacza to, że na płytę o powierzchni 1 metra kwadratowego można postawić 30 ton. Przeciętny dom jednorodzinny (zwykle o powierzchni 100-200 m²) wywiera nacisk na fundamenty rzędu kilkunastu do kilkudziesięciu ton na metr bieżący ławy, a nie na metr kwadratowy izolacji pionowej. Jednak pod ławami (gdzie też można stosować specjalne, wytrzymałe płyty XPS jako izolację podłogi na gruncie) czy pod ścianami fundamentowymi, naciski na materiał mogą być znaczne. Wytrzymałość XPS-u jest z nawiązką wystarczająca do roli szalunku bocznego i izolacji pionowej ław fundamentowych.
Myśl analityczna podpowiada, że wybór materiału na szalunek tracony powinien opierać się na jego wielofunkcyjności. XPS nie tylko formuje beton, ale staje się częścią izolacji budynku. Eliminuje potrzebę późniejszego oklejania fundamentów styropianem (EPS) czy inną izolacją, oszczędzając czas i materiały. To sprytne połączenie funkcji w jednym produkcie.
Przykład z życia wzięty: Widziałem budowę, gdzie po rozszalowaniu drewnianego fundamentu, wykonawca zaczął oklejać ściany fundamentowe 10 cm EPS-em. Zajęło im to kolejne półtora dnia pracy. Gdyby od razu zastosowali szalunek XPS o grubości 10 cm, ten etap byłby już zakończony wraz z betonowaniem. Prosta arytmetyka czasu i pracy.
Wykres powyżej prezentuje orientacyjne porównanie kosztów związanych z różnymi metodami szalowania fundamentów na przykładzie 100 metrów bieżących. Dane mają charakter poglądowy i opierają się na uśrednionych szacunkach cen materiałów oraz koszcie pracy (przy założeniu stawki godzinowej). Warto zauważyć, że choć materiał XPS ma wyższą cenę zakupu, oszczędność czasu montażu (wyrażona jako ekwiwalent kosztu pracy, ponieważ nie ma rozszalowania) znacząco wpływa na ogólny bilans. To pokazuje, jak ważna jest analiza całego procesu, a nie tylko ceny jednego komponentu. Czas to pieniądz, a na budowie to podwójnie prawda.
Widzimy na wykresie, że początkowa inwestycja w materiał XPS jest wyraźnie wyższa niż w przypadku tradycyjnego drewna czy wynajmu systemu. Jednak po doliczeniu kosztów pracy związanych z rozszalowaniem i sprzątaniem w przypadku metod tradycyjnych, oraz po uwzględnieniu oszczędności czasu przy montażu XPS, różnica w całkowitych kosztach "etapu zero" maleje lub nawet znika. Prawdziwą korzyścią finansową szalunku XPS są jednak oszczędności generowane przez lata na ogrzewaniu dzięki wbudowanej, trwałej izolacji. Tego wykres "etapu zero" nie pokazuje, ale jest to klucz do zrozumienia opłacalności rozwiązania w długim okresie. Myśląc strategicznie, ten wykres to tylko część historii.
Podsumowując nasze rozważania o właściwościach XPS w kontekście szalunku traconego, mamy do czynienia z materiałem o parametrach, które doskonale wpisują się w potrzeby nowoczesnego budownictwa energooszczędnego. Jest to trwałe, skuteczne i funkcjonalne rozwiązanie, które zmienia sposób myślenia o izolacji fundamentów, integrując ją z samym procesem ich powstawania. To rewolucja w drobnej skali, dostępna dla każdego inwestora, który myśli długoterminowo i ceni sobie jakość oraz efektywność energetyczną swojego przyszłego domu.